COSTAR Project
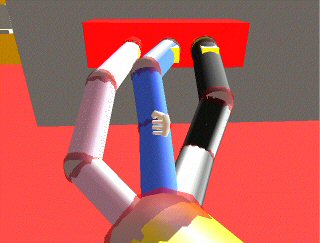
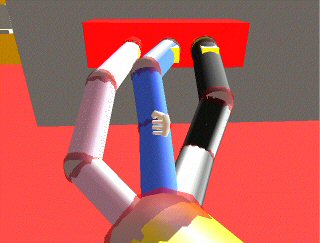
The aim of the COSTAR 1 project was to enable the early integration of cable harness design into electro-mechanical design through the use of cognitive engineering techniques and virtual reality (VR) technologies. The first part of the project ran from 1st October 2001 until 31st September 2004, and was based on two previous projects that investigated the use of VR in assembling planning and routing cable harnesses. The second part of the project ran from 1st October 2004 until the present and is based on improving the hardware and software to giv more functionality. The research goals involve using the COSTAR environment to investigate a number of issues regarding cable harness design in a virtual environment. These can be summarised by considering CO-STAR from several viewpoints:
-
COSTAR as part of the electro-mechanical product development process
-
COSTAR as a design environment for cable harnesses
-
COSTAR as a vehicle to evaluate human factors of working within virtual reality environments
-
COSTAR as an environment for capturing design intent
Objectives for the 1st part of the project are listed as:
1. Generate a method to represent and deliver necessary manufacturing data from the VR interface.
2. Establish a method to represent and manage information relating to multiple cables that form a cable harness.
3. Compare and contrast virtual design task with CAD, mixed reality, augmented reality methods. This work involves benchmarking the prototype immersive VR tool with traditional CAD equivalents and other non-VR methods.
4. Validate research results through trials in conjunction with industrial user partners.
Objectives for the 2nd part of the project are listed as:
5. Redevelopment of the user logging facility to allow subsequent analysis of the data to be more automated. - Previous analysis of the user log files were performed manually so was both time-consuming and laborious. To overcome this, the structure of the log files required to be changed and more information had to be recorded into the log file. This allowed the total time spent on each type of design task to be calculated and automatically plotted. In addition, repeating patterns of activity could be identified to help determine what is the best practice for particular design tasks.
6. Move to a more powerful VR hardware platform to give a more immersive experience. - This involved moving from an SGI Octane2 workstation to an SGI Onyx4 visualisation system to increase the computing and graphical power. This will allow a more realistic VR environment to be developed and more functionality can be incorporated into the system without overloading the hardware.
7. Perform user trials to obtain feedback on the VR design system and to analyse the generated log files. - A trial involving 10 users were carried out and involved the participants performing several design tasks and being logged unobtrusively in the background.
8. Incorporate the user logging tools into the Grand Challenge project. - Having applied the user logging functionality in a 3D immersive design environment, the next step was to apply the same techniques to a traditional 2D CAD-like design environment. Due to the difficulty in obtaining access to the source code of commercial CAD packages, a design application called BAMZOOKi was selected as the platform to test the logging tools.
9. Extraction and formalisation of design knowledge. - By using a spreadsheet macro to parse the log files, IDEF0 diagrams can be automatically plotted to allow the design processes to be visualised and formalised. This formalised design knowledge can then be utilised in an information push system, which is integrated into the design environment, where the system can identify what task the user is carrying out and relevant information can displayed to the user if assistance is required.
![]() ![]() |
![]() ![]() |
![]() ![]() |
![]() ![]() |